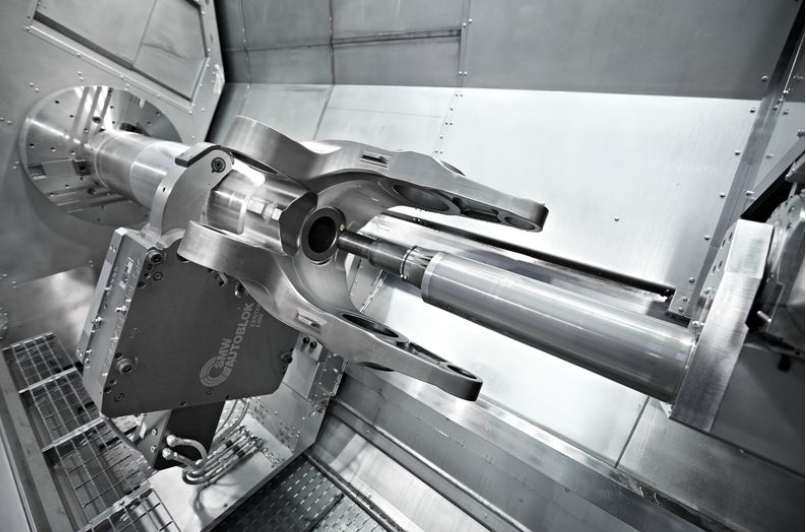
Since their inception in the 1950s, titanium alloys have redefined the boundaries of material science, emerging as indispensable structural metals across cutting-edge industries. These remarkable composite materials, crafted by blending titanium with strategic elements, boast an unrivaled combination of strength, lightness, and resilience. From soaring aircraft to life-changing medical implants, titanium alloys power innovation with their extraordinary properties: an exceptional strength-to-weight ratio, unparalleled corrosion resistance, and steadfast performance under extreme temperatures. The aviation industry alone accounts for roughly 50% of global demand, relying on these alloys for airframe structures and critical engine components that demand precision and durability.
Properties of Titanium Alloys
1. Strength That Defies Gravity
Titanium alloys are the superheroes of structural metals, delivering strength rivaling high-strength steel while weighing only 57% as much. This extraordinary strength-to-weight ratio is a game-changer for aerospace applications, slashing aircraft weight and boosting fuel efficiency. Every gram saved translates to longer flights, lower costs, and a reduced environmental footprint.
2. Thriving in the Heat of the Moment
When temperatures climb to 400–500°C, titanium alloys remain unfazed, retaining their mechanical integrity where lesser materials falter. Specialized variants can even endure short bursts above 600°C, making them the go-to choice for the scorching environments of aircraft engines. From turbine blades to exhaust systems, these alloys ensure reliability under fire.
3. Corrosion Resistance
Titanium alloys laugh in the face of corrosion. A naturally forming, dense oxide film shields them from acids, alkalis, saltwater, and harsh chemical environments. This resilience makes them indispensable in marine engineering, chemical processing, and offshore applications. Enhanced by oxide, nitride, and carbide layers, their durability is nothing short of legendary.
4. Harmony with the Human Body
In the medical realm, titanium alloys shine as biocompatible marvels. Their compatibility with human tissue eliminates rejection risks, making them the gold standard for artificial joints, dental implants, and surgical hardware. Patients regain mobility and quality of life, thanks to materials that integrate seamlessly with the body.
Challenges of Machining Titanium Alloys
While titanium alloys are engineering marvels, machining them is no walk in the park. Their unique properties present formidable challenges that demand precision, expertise, and innovation.
1. Heat That Tests Endurance
With thermal conductivity just 16% that of 45# steel, titanium alloys trap heat during machining, causing cutting zone temperatures to soar, sometimes doubling those seen in steel machining. This accelerates tool wear, testing the limits of even the toughest equipment.
2. Work Hardening That Fights Back
Titanium alloys harden significantly during machining, forming tough surface layers that resist subsequent cuts. This work hardening outpaces even stainless steel, increasing tool damage and slashing efficiency. Every pass becomes a battle against the material’s defenses.
3. Chemical Reactions That Wear Tools Down
At high temperatures, titanium alloys bond chemically with tool materials, causing adhesive wear that shortens tool life. Their machinability is a mere 20% of free-cutting steel, making every cut costly.
4. Vibrations That Threaten Precision
The low elastic modulus of titanium alloys leads to elastic deformation and vibrations during machining. These disruptions compromise precision and surface quality, demanding meticulous control to achieve the desired finish.
Optimization Strategies for Titanium Alloy Machining
To conquer the challenges of titanium cnc machining, engineers employ a blend of advanced tools, optimized parameters, and cutting-edge cooling techniques. Here’s how the pros do it:
1. Precision Turning for Flawless Results
- Tool Selection: Carbide tools like YG6, YG8, or YG10HT offer the durability needed to tackle titanium’s toughness.
- Geometry Parameters: Larger clearance angles (10–15°) and reduced rake angles (5–8°) minimize heat buildup, with a tool nose radius of 0.5–1mm for smooth cuts.
- Cutting Parameters: Low speeds (30–50 m/min), moderate feeds (0.1–0.3 mm/r), and deeper cuts (2–5 mm) balance efficiency and tool longevity.
- Cooling Method: High-pressure coolant (10–20 MPa) floods the cutting zone, dissipating heat and extending tool life.
- Operational Precision: For pristine finishing, align the tool tip precisely with the workpiece center and use a 75–90° lead angle.
2. Milling with Mastery
- Milling Method: Climb milling reduces tool wear and enhances surface quality.
- Tool Material: High-performance high-speed steel (M42) or ultra-fine grain carbide ensures durability.
- Geometry Improvements: Reduced rake angles (0–5°) and increased clearance angles (12–16°) optimize performance.
- Cutting Parameters: Speeds of 20–40 m/min and feeds of 0.05–0.15 mm/tooth maintain control.
- Tool Selection: Sharp-edged milling cutters outperform form-relieved designs, delivering cleaner cuts.
3. Tapping with Finesse
- Tap Selection: Skip-tooth taps with 2–3 teeth and a chamfer angle spanning 3–4 thread pitches reduce resistance.
- Geometry Improvements: Negative rake angles on chamfers and increased back taper enhance chip evacuation.
- Operational Points: Shorter taps boost rigidity, while ample cooling and lubrication prevent seizing.
- Process Parameters: Speeds of 2–5 m/min, paired with high-lubricity cutting fluid, ensure smooth tapping.
4. Comprehensive Solutions for Thermal Mastery
At the heart of titanium alloy machining lies one critical challenge: heat management. A holistic approach is key:
- Advanced Tooling: Select tool materials with TiAlN coatings to resist wear and heat.
- Optimized Geometry: Fine-tune tool angles to minimize heat generation without sacrificing strength.
- High-Pressure Cooling: Deploy 15–20 MPa cooling systems to keep temperatures in check.
- Balanced Parameters: Choose cutting speeds and feeds that maximize efficiency while preserving tool life.
- Specialized Fluids: Develop cutting fluids tailored for superior cooling and lubrication.
Future of Titanium Alloys
By integrating advanced tools, precise parameters, and innovative cooling systems, manufacturers can unlock the full potential of titanium alloys. These strategies enhance machining efficiency and ensure consistent quality, meeting the soaring demand for titanium components in aerospace, medical, and industrial applications. As industries push the boundaries of performance and sustainability, titanium alloys stand ready to shape the future, one precision-crafted part at a time.