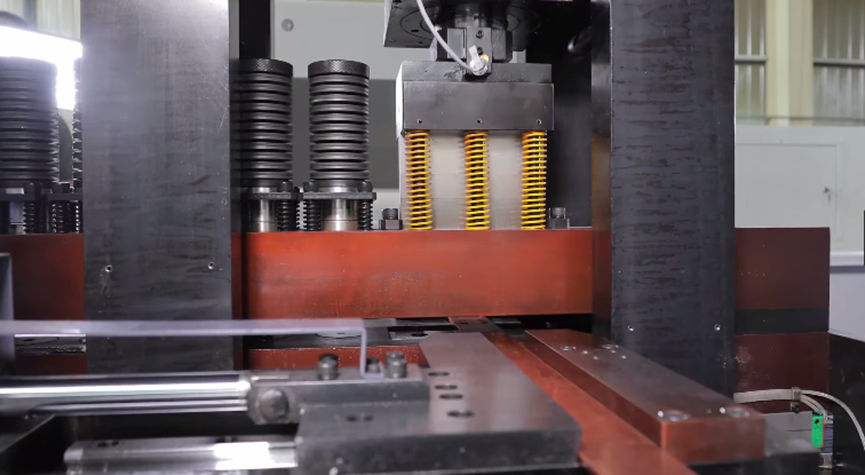
Cutting Technology: The Evolution of Shearing Technology in Modern Busbar Processing
The humble busbar remains a critical component in today’s rapidly evolving electrical distribution industry. These metal strips or bars, typically made of copper or aluminum, are the backbone of electrical switchgear, switchboards, and distribution systems. As power demands increase and electrical systems become more complex, the technologies used to manufacture these important components have also undergone significant changes.
Shearing technology, in particular, has made significant advances that have revolutionized the way busbar is cut, formed, and prepared for installation. This blog post explores cutting-edge innovations that are reshaping the busbar manufacturing landscape and driving new levels of precision, efficiency, and reliability.
The Critical Role of Busbar Cutting
Before diving into these innovations, it’s important to understand the importance of precision cutting. Busbars typically carry large amounts of current in a confined space, and tolerances are measured in millimeters. Improper busbar cutting can result in poor connections, increased resistance, overheating, and ultimately system failure. In high-power applications, these failures can be catastrophic, causing equipment damage, production downtime, and even electrical fires.
Traditional cutting methods often produce rough edges, burrs, and dimensional inconsistencies that require additional finishing. Modern shearing technology aims to eliminate these issues through innovations that improve accuracy, repeatability, and surface quality.
CNC Integration: The Brains Behind Modern Shearing
The most transformative innovation in busbar cutting is the integration of computer numerical control (CNC) systems. These advanced control mechanisms have elevated busbar cutting from a manual craft to a precision science.
Today’s advanced CNC busbar machine support 2D and 3D drawing imports, allowing operators to visualize the finished busbar before cutting begins. The MAC MX602K-8C CNC punching and shearing machine can be remotely accessed via WIFI and LAN connections, allowing real-time monitoring and adjustments. This connectivity also facilitates integration with broader Manufacturing Execution Systems (MES) and Enterprise Resource Planning (ERP) platforms.
Where modern CNC shearing systems really stand out is in their ability to automatically calculate the precise locations of punching, shearing, and folding operations. This eliminates human error in manual coding and significantly reduces material waste. Some systems can even virtually demonstrate the entire manufacturing process before any metal is cut, acting both as a verification tool and as a training aid for operators.
Revolutionary Shearing Mechanism
The innovative shearing mechanism redefines the physics of cutting, making it possible to achieve cleaner, more precise cuts with less deformation. The “integral scissors” design represents a major leap forward, completing the cut in one operation while maintaining excellent verticality of the busbar cut.
The SUNSHINE busbar machine uses a “sleeve-to-sleeve” shearing concept that supports both the ID and OD of the material throughout the cutting process. This approach achieves clean, burr-free cuts with minimal deformation – critical for processing soft metals such as copper and aluminum.
These innovations address one of the most persistent challenges in busbar manufacturing: maintaining dimensional accuracy while avoiding material deformation that can affect electrical performance. By achieving a clean cut with vertical edges, modern shearing technology eliminates the need for secondary finishing, reducing time and labor costs.
Advanced Die Library and Tool Stations
Busbar punching machine are equipped with advanced die libraries and multiple tool stations that significantly expand their capabilities. The MAC MX602K-8C CNC busbar punching and shearing machine can accommodate up to nine die stations, including specialized dies for shearing, embossing, and punching operations.
The single-row die library design, with configurations such as “7 punching + 1 shearing + 1 embossing”, ensures perfect concentricity between different processes. This alignment is critical to maintaining the electrical and mechanical integrity of the finished bus duct.
The modern die design has excellent durability, and some dies are rated to withstand up to 50,000 impacts without replacement. This long life, coupled with a quick-change system, minimizes downtime during die changes, helping to improve the overall efficiency and economy of bus duct production.
Servo-driven precision
The integration of servo motor technology represents another leap forward in shearing precision. Today, CNC busbar cutting machines have adopted servo systems from high-end manufacturers such as Rexroth of Germany, achieving positioning accuracy as low as ±0.20 mm per meter of length.
A servo-driven material stop ensures that each busbar is positioned with precise repeatability, while a servo clamping system maintains precise alignment during the cutting process. This precision is particularly important when manufacturing busbars for high-current applications, as even small dimensional variations can affect electrical performance.
The closed-loop feedback system in modern servo control systems continuously monitors position, force and speed, and makes real-time adjustments to maintain optimal cutting conditions. This adaptive ability is particularly important when processing materials of varying thickness or hardness.
Advances in hydraulic power
The power behind modern shearing operations comes from advanced hydraulic systems that provide precisely controlled force. Modern hydraulic stations use high-quality motors (such as ABB of Switzerland) and can generate up to 600 kN of pressure – enough for busbar cutting machines to easily cut the thickest copper or aluminum busbars.
What distinguishes these systems from their predecessors is their advanced pressure and flow control. The dual-speed, dual-pressure configuration enables fast approach speeds followed by precisely controlled cutting speeds. This optimized cycle minimizes operating time while maximizing cut quality.
Modern hydraulic systems also integrate advanced filtration and cooling systems to extend fluid life and ensure consistent performance. Some manufacturers have developed environmentally friendly hydraulic solutions using biodegradable fluids to address growing concerns about sustainability in the manufacturing industry.
Integrated Production Solutions
Perhaps the most significant paradigm shift is the move toward fully integrated production lines. Modern busbar cutting machine can be seamlessly connected with bending and punching processes to create comprehensive manufacturing cells.
These integrated systems allow production programs to be shared in real time via WIFI or LAN connections, ensuring perfect synchronization between different processes. The entire production process of busbars from raw materials to finished products requires little to no human intervention, significantly reducing handling time and the potential for damage.
Some manufacturers have developed unified control interfaces that allow operators to program the entire manufacturing process at a single workstation. These intuitive interfaces reduce training requirements and minimize the potential for programming errors.
Software Intelligence
The software that drives modern busbar cutting systems has become very sophisticated. In addition to basic CNC functions, today’s systems also use advanced algorithms that can optimize cutting sequences, minimize material waste, and adapt to different material properties.
Beckhoff control systems with closed-loop feedback have high control accuracy and strong anti-interference capabilities. Their flexible adaptive functions can adjust cutting parameters in real time based on material resistance, temperature and other factors that may affect cutting quality.
Some systems now integrate artificial intelligence components that can learn from previous operations and continuously optimize cutting parameters for the best results. This machine learning capability represents the forefront of busbar manufacturing technology.
Improved efficiency and sustainability
The cumulative effect of these innovations has significantly improved machining efficiency. Modern CNC busduct machines can cut at speeds of up to 75 meters per minute with minimal waste. Center shear cutters ensure clean cuts with no waste, smooth burr-free surfaces and no need for secondary finishing.
These efficiency gains translate directly into economic and environmental benefits. Faster production means lower labor costs per piece, while reduced waste helps save materials and achieve sustainability goals. The precision of modern cutting systems also reduces scrap rates, further improving overall production efficiency.
Conclusion
Innovations in busbar shearing technology are more than incremental improvements to existing processes. They fundamentally reshape how these important components are manufactured, with transformative impacts on quality, efficiency, and reliability.
For electrical system designers and manufacturers, these advances offer new possibilities for creating more compact, efficient, and reliable distribution systems. For end users, these advances mean safer electrical installations that last longer and require less maintenance.
As the demand for electricity continues to grow and power systems become more complex, the importance of precision-manufactured busbars grows. The cutting-edge shearing technologies discussed in this article will play a key role in meeting these challenges and enabling the development of next-generation distribution systems.