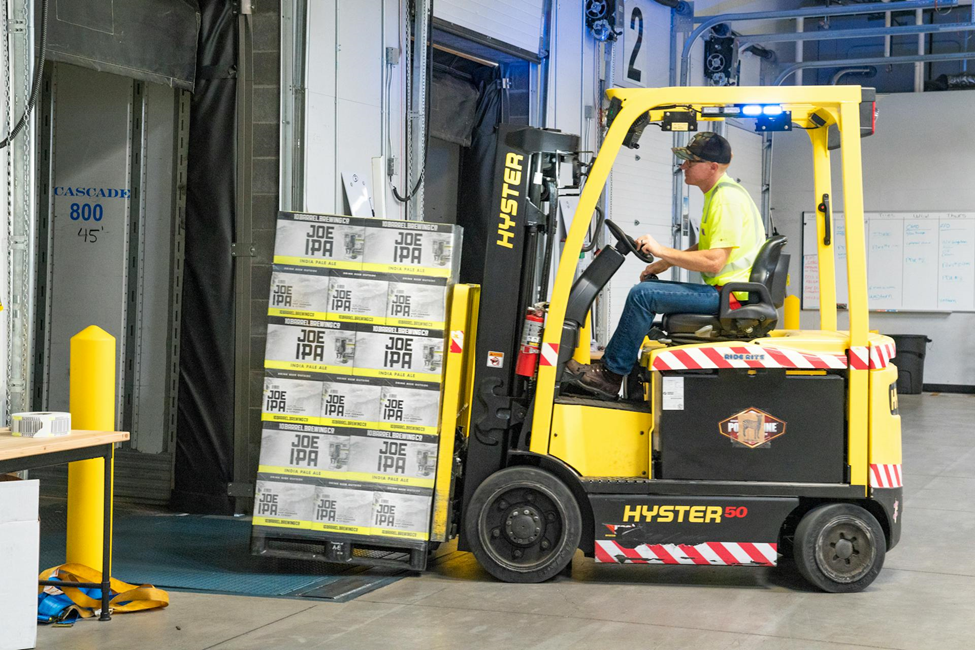
When customers walk into a store or place an online order, they rarely think about the maze of operations that led to that moment. Yet behind every product on a shelf or doorstep lies a sophisticated network of warehouse systems quietly keeping everything running. In retail, the warehouse isn’t just storage — it’s the engine room. Poorly managed warehouses lead to stockouts, delays, and unhappy customers. Efficient ones drive profit, loyalty, and growth.
As e-commerce grows and expectations for fast delivery rise, optimizing warehouse operations has become more urgent than ever.
This article dives into some effective strategies retailers can adopt to streamline operations, reduce waste, and boost performance.
1. Maintain Essential Equipment
Warehouse equipment plays a critical role in daily operations, and none more so than the humble forklift. These machines move heavy loads across large spaces, and when one breaks down, the entire flow of goods can stall.
Preventive checks should be part of a routine, with operators flagging issues early and technicians addressing wear before it turns into failure. In addition to scheduled inspections, it’s important to use quality replacement parts. This is where trusted suppliers like Intella Parts come in. Known for their wide range of cost-effective forklift parts, Intella serves major brands like Toyota, Hyster, and Crown. Their website, www.intellaparts.com, allows easy search by part number or make, and their customer support is known for being responsive and helpful.
Investing in reliable parts doesn’t just prevent downtime. It also extends the lifespan of your equipment, improves safety, and reduces emergency repair costs. Skimping on quality today often leads to bigger bills tomorrow.
2. Prioritize Real-Time Inventory Accuracy
In retail, inventory is money sitting on a shelf. If the numbers are off, everything else becomes harder, whether it’s planning promotions, reordering stock, or fulfilling online orders. Relying on manual counts or outdated systems creates blind spots that can lead to stockouts, overstock, or missed opportunities.
Real-time inventory tracking solves this by providing up-to-date visibility across your entire operation. Using barcodes or RFID tags, warehouse staff can scan items as they move in and out, syncing data immediately to the inventory management system.
Getting inventory right is not just about accuracy; it’s about control. With it, you can forecast demand better, fulfill orders faster, and reduce the amount of capital locked up in excess stock.
3. Layout Design: Make Every Step Count
The physical design of a warehouse directly impacts how efficiently people and goods move. A poor layout forces workers to travel longer distances, take awkward routes, or deal with traffic bottlenecks. That adds time, stress, and mistakes.
An efficient layout starts with understanding your workflows. High-volume items should be stored closer to the packing and shipping areas. Receiving docks should be clear and easy to access. Narrow aisles save space but must still allow safe forklift movement. Using vertical space with high racks can also help maximize storage without expanding the footprint.
4. Invest in Warehouse Management Software (WMS)
Manual processes slow things down and invite errors. A warehouse management system automates the tracking of inventory, orders, shipments, and worker productivity. It can optimize picking routes, flag when items need restocking, and even suggest better slotting for fast-moving products.
Many WMS platforms integrate with online storefronts and ERPs, ensuring a consistent flow of data. This improves accuracy and reduces double-entry work. For growing operations, the right software can replace hours of manual labor each week.
5. Streamline the Picking Process
Order picking is one of the most labor-intensive tasks in any warehouse. Without structure, workers can waste time walking aimlessly or grabbing the wrong items. A streamlined picking system reduces movement, increases speed, and cuts errors.
Strategies like batch picking allow workers to gather multiple orders in one trip. Zone picking assigns areas to individuals, avoiding overlap. Technology like handheld scanners or voice-guided systems provides instructions in real-time, reducing the need to reference paper lists.
The less time workers spend figuring things out, the more time they spend moving orders forward.
6. Train and Cross-Train Your Staff
Warehouse technology is powerful, but people remain at the heart of every operation. Well-trained employees make fewer mistakes, move more confidently, and keep the workflow steady even under pressure.
Structured onboarding is the first step. New hires should understand warehouse layout, safety procedures, equipment use, and system tools. But training shouldn’t stop there. Ongoing refreshers and updates help employees keep pace with changes, especially during software upgrades or layout changes.
Cross-training is equally important. When staff can fill in for one another, you gain flexibility. During busy periods or staff shortages, cross-trained employees can shift roles without slowing operations.
7. Build a Safety-First Culture
Employees need to feel protected and valued. Warehouses are full of potential hazards: moving machinery, stacked pallets, slippery floors, and tight spaces. A single incident can cause serious injury and derail operations.
The most effective safety programs are part of the everyday culture, not just an annual training session. Post clear signage throughout the facility. Ensure walkways are free from obstructions. Perform regular equipment inspections. Above all, make sure everyone wears proper gear and knows how to use tools safely.
8. Plan for Seasonal and Sudden Surges
Retail doesn’t run on a steady schedule. Sales rise and fall with the seasons, holidays, and unpredictable trends. If your warehouse only works under ideal conditions, you’ll struggle when demand spikes. The solution is to build flexibility into your planning.
Look at historical sales data to predict peak periods. Stock up early on bestsellers, and prep overflow space to handle temporary volume increases. Have a roster of trained temp workers ready to call in during busy months. Invest in mobile shelving or collapsible packing stations that can expand capacity when needed.
Sudden surges—like a viral product or supply chain disruption—are harder to predict. That’s why having solid vendor relationships, quick access to equipment, and adaptable staff matters.
Optimizing warehouse operations doesn’t require massive investments. Instead, it comes down to practical, ongoing decisions that focus on accuracy, efficiency, and reliability.
In today’s competitive retail environment, the best experiences don’t start at the store or checkout page—they start at the warehouse. And the businesses that get it right behind the scenes will lead from the front.