The cornerstone of effective material handling in various industries is undeniably tied to the efficiency of conveyor systems. These systems are the lifelines of manufacturing and distribution operations, enabling the swift, safe, and reliable transport of goods across different stages of production and delivery. Integral to this efficiency are components like Conveyor Impact Rollers, Heavy Duty Roller Conveyors, and Nylon Conveyor Rollers, each playing a unique role in optimizing the conveyor’s performance. Conveyor Impact Rollers absorb shocks and distribute loads evenly, minimizing wear and tear on the system. Heavy Duty Roller Conveyors are engineered to handle the most demanding loads, ensuring durability and continuous operation under heavy use. Meanwhile, Nylon Conveyor Rollers provide a lightweight, corrosion-resistant option that reduces maintenance needs and enhances the system’s longevity. Together, these components ensure that conveyor systems can meet the high demands of modern industry, maximizing throughput and minimizing downtime.
Impact Rollers: Maximizing Conveyor Performance
How Conveyor Impact Rollers Absorb Shock and Protect Materials During Transfer
At the heart of enhancing conveyor system performance and durability is the Conveyor Impact Roller, a pivotal component designed to absorb the considerable shock and impact that can occur during the transfer of materials. These rollers are strategically positioned at the conveyor’s loading points, where materials are dropped onto the belt, often from a height. The primary function of a Conveyor Impact Roller is to serve as a buffer between the falling materials and the conveyor belt itself, effectively dissipating the energy and force of the impact.
Conveyor Impact Rollers are constructed from robust materials capable of withstanding significant abuse without compromising their integrity. The outer layer, often made from a blend of rubber or specialized composites, is engineered to be both resilient and durable. This layer acts to absorb the shock of impacting materials, minimizing the risk of damage not just to the conveyor belt but also to the materials being transported. This absorption capability is crucial for maintaining the integrity of the conveyor belt over time, preventing tears, punctures, or other forms of wear that could necessitate costly repairs or replacements.
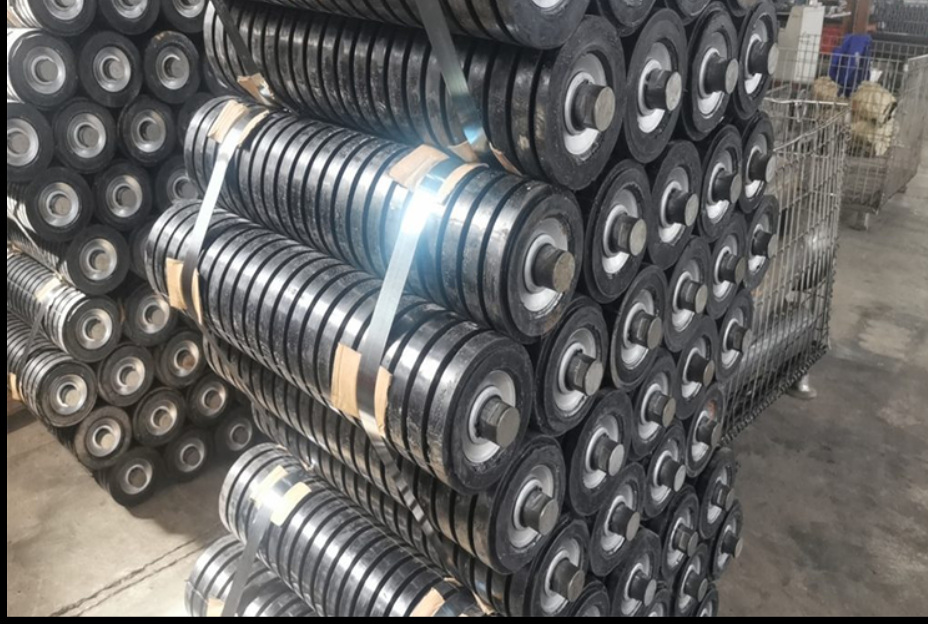
Moreover, the presence of Conveyor Impact Rollers helps ensure that materials are deposited onto the conveyor belt in a controlled manner. By softening the impact of the drop, these rollers contribute to a smoother transfer process, reducing spillage and the potential for material breakage. This not only aids in protecting the conveyor system but also ensures that the materials being transported maintain their quality and integrity, crucial in industries where the condition of the product is paramount.
In essence, Conveyor Impact Rollers play an indispensable role in maximizing conveyor performance. Their ability to absorb shock and protect materials during transfer points contributes significantly to the efficiency and longevity of the conveyor system. By mitigating the effects of high-impact forces, these rollers ensure that the conveyor can operate smoothly and continuously, supporting the seamless flow of operations and ultimately enhancing productivity.
Heavy Duty Roller Conveyors for Industrial Applications
Heavy Duty Roller Conveyor is indispensable in the realm of industrial applications, designed specifically to handle heavy loads with efficiency, durability, and reliability. These conveyors are engineered to meet the rigorous demands of various industries, facilitating the movement and management of large, heavy items across numerous sectors. The design elements and benefits of Heavy Duty Roller Conveyors make them a vital component in optimizing industrial operations, enhancing productivity, and reducing operational costs.
The Design of Heavy Duty Roller Conveyors
Robust Materials:The construction of Heavy Duty Roller Conveyors utilizes high-grade, robust materials such as thick steel or reinforced aluminum for frames and rollers. These materials ensure the conveyors can withstand heavy loads, impacts, and the rigors of industrial environments without significant wear and tear.
Large Diameter Rollers:These conveyors feature rollers with larger diameters than those found in standard conveyors, which distribute the weight of heavy loads more evenly. This design minimizes the pressure on any single point, reducing wear and extending the life of the conveyor.
High Load Capacity:Engineered for high performance, Heavy Duty Roller Conveyors are designed with a high load capacity in mind. This allows them to move heavy industrial products, equipment, and materials efficiently, supporting the operational needs of various industries.
Customization and Flexibility:To accommodate the specific needs of different industrial applications, Heavy Duty Roller Conveyors can be customized in terms of length, width, roller diameter, and spacing. Additional features such as adjustable speeds, side guides, and accumulation zones can also be integrated to enhance functionality.
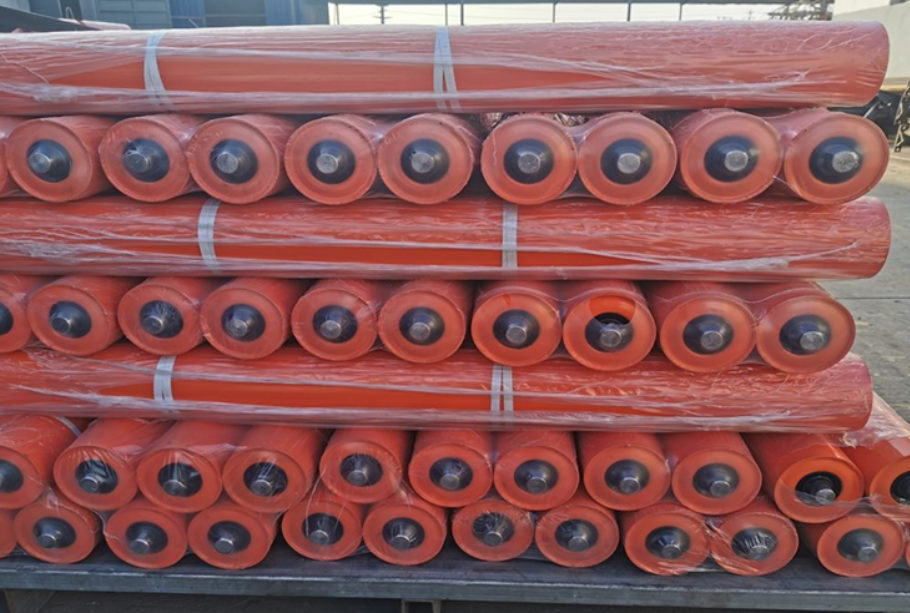
Benefits of Heavy Duty Roller Conveyors in Handling Heavy Loads
Increased Efficiency:By enabling the smooth and continuous movement of heavy loads, these conveyors significantly increase operational efficiency. They reduce the need for manual handling, speeding up the process of moving goods from one point to another within industrial settings.
Enhanced Safety:The use of Heavy Duty Roller Conveyors minimizes the risk of workplace injuries associated with manual lifting and moving of heavy objects. This not only protects employees but also reduces potential downtime and associated costs due to injuries.
Durability and Longevity:Thanks to their robust design and construction, these conveyors are highly durable and have a long operational life. This durability ensures that they can handle the continuous demands of heavy industrial use, providing a reliable solution for material handling over the long term.
Cost-Effectiveness:While the initial investment in a Heavy Duty Roller Conveyor may be higher than that of a standard conveyor, the long-term savings in maintenance, repair costs, and improved efficiency make it a cost-effective solution for industrial applications.
Heavy Duty Roller Conveyors are designed with the challenges of industrial applications in mind, offering a solution that is not only capable of handling heavy loads but also improving operational efficiency, enhancing workplace safety, and providing long-term reliability. Their robust design, combined with the ability to customize features to meet specific industrial needs, makes them an invaluable asset in the transportation and handling of heavy materials and products. Whether in manufacturing, distribution, or any other sector where heavy loads are a commonality, Heavy Duty Roller Conveyors provide a robust, efficient, and safe material handling solution.
Incorporating Nylon Conveyor Rollers for Versatility
The integration of Nylon Conveyor Rollers into material handling systems significantly enhances their efficiency and adaptability. Known for their lightweight and durable characteristics, these rollers present a pivotal advancement in the design and operation of conveyor systems. The inherent properties of nylon, including its high strength-to-weight ratio and excellent wear resistance, contribute to the overall performance and reliability of conveyor systems.
Lightweight and Durable Nature
Nylon Conveyor Rollers are celebrated for their lightweight nature, which makes them easier to install, handle, and maintain compared to their metal counterparts. This reduction in weight does not compromise their strength or durability. In fact, nylon’s resilience under varying operational conditions reduces the incidence of roller failure, thereby minimizing downtime and maintenance requirements. The lightweight design also contributes to lower energy consumption, as conveyor systems require less power to move materials, further enhancing operational efficiency.
Impact on System Efficiency
The efficiency of a conveyor system is significantly influenced by the performance of its rollers. Nylon Conveyor Rollers, with their smooth surface and reduced friction, facilitate the seamless movement of materials across the conveyor belt. This efficiency reduces the strain on the conveyor motor and prolongs the life of both the belt and the rollers themselves. Additionally, the anti-corrosive properties of nylon ensure that these rollers can withstand environments that are detrimental to metal rollers, such as those with high moisture or chemical exposure.
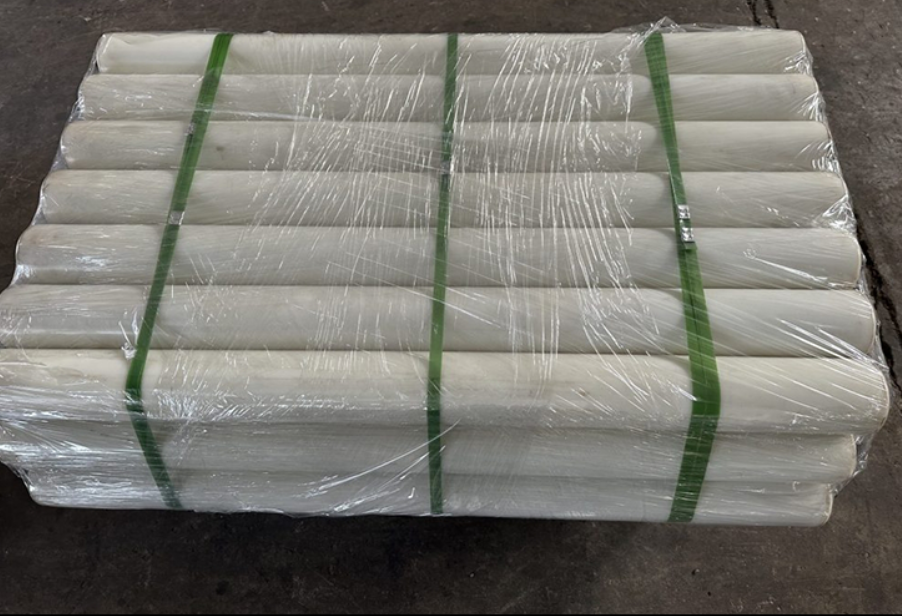
By incorporating Nylon Conveyor Rollers, industries can achieve a versatile conveyor system that is capable of handling a wide range of materials under various environmental conditions. Their durability and lightweight design contribute to a reduction in operational costs, making them a cost-effective solution for enhancing the efficiency and longevity of conveyor systems.
Combining Components for Optimal System Performance
In the realm of conveyor systems, achieving optimal performance requires a strategic approach to selecting and combining various components. Specifically, the integration of Conveyor Impact Rollers, Heavy Duty Roller Conveyors, and Nylon Conveyor Rollers can significantly enhance the efficiency, durability, and functionality of the system. This section explores strategies for effectively combining these components to meet the diverse needs of industrial applications, ensuring a conveyor system that is not only robust but also versatile and efficient.
Strategic Integration of Conveyor Components
Identifying Load Requirements:The first step in combining components for optimal performance is to identify the specific load requirements of the conveyor system. Heavy Duty Roller Conveyors are ideal for handling large, heavy loads typically found in industries such as manufacturing and mining. For areas of the conveyor system subjected to high impact loads, such as loading zones, Conveyor Impact Rollers are essential for absorbing shock and protecting the system. Meanwhile, Nylon Conveyor Rollers offer a lightweight, corrosion-resistant option for environments requiring clean, quiet operation, such as food processing or pharmaceuticals.
Zone Customization:Instead of a one-size-fits-all approach, segmenting the conveyor system into zones based on the specific tasks and environmental conditions can greatly improve efficiency. For example, integrating Conveyor Impact Rollers at loading zones to absorb the initial impact of heavy items can prevent damage to both the conveyor belt and other components. Heavy Duty Roller Conveyors can be utilized in the main transport sections where the strength and durability to move heavy loads are paramount. Nylon Conveyor Rollers could be used in the final sections of the conveyor system, where lighter loads need to be moved quietly and smoothly to their destination.
Balancing Cost and Performance:Combining these different types of rollers allows for a balanced approach to cost and performance. By strategically placing more expensive, specialized components like Heavy Duty and Impact Rollers only where they are most needed and utilizing cost-effective Nylon Rollers in less demanding sections, overall system costs can be optimized without compromising performance.
Maintenance and Longevity:Each component within the conveyor system—Conveyor Impact Rollers, Heavy Duty Roller Conveyors, and Nylon Conveyor Rollers—has its maintenance requirements and lifespan. Designing the system with these factors in mind ensures that maintenance is manageable and does not significantly disrupt operations. For instance, placing easy-to-maintain Nylon Rollers in hard-to-reach areas can reduce maintenance time and costs.
Enhancing Overall System Efficiency
The combination of Conveyor Impact Rollers, Heavy Duty Roller Conveyors, and Nylon Conveyor Rollers, when done strategically, leads to a highly efficient conveyor system tailored to the unique needs of the operation. This approach not only extends the lifespan of the conveyor system by ensuring that each component is used in the most appropriate context but also enhances operational efficiency by optimizing the conveyor for different types of loads and environmental conditions. Furthermore, it contributes to safety and reduces operational costs by minimizing the risk of system failure and downtime.
In conclusion, achieving optimal performance in a conveyor system is not simply about choosing the highest quality components but rather about strategically combining different types of rollers to meet the specific needs of the operation. By carefully considering the load requirements, environmental conditions, and operational goals, it is possible to design a conveyor system that is both cost-effective and capable of handling the demands of industrial applications with exceptional efficiency and reliability.