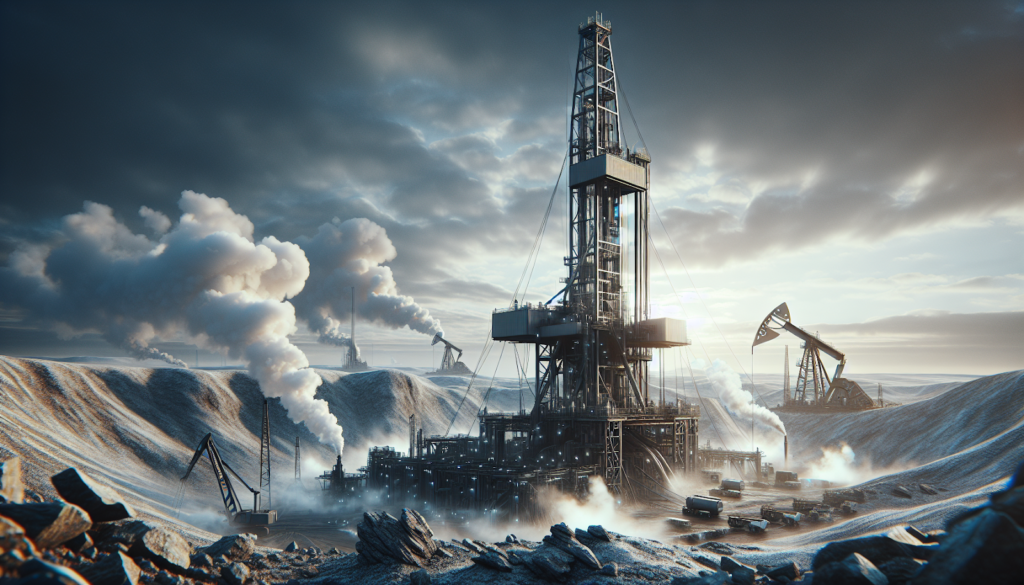
The quest for sustainable and renewable energy sources has led to a significant focus on geothermal energy. Buried beneath the Earth’s crust, geothermal energy offers a steady and environmentally-friendly power source. However, unlocking this source of power requires specialized drilling techniques that can penetrate deep into the hot rock reservoirs. The role of effective BTA Drilling in geothermal extraction cannot be overstated; it is the pathway through which we access the Earth’s natural geothermal resources. Consequently, the tools, technologies, and practices used in this undertaking are of paramount importance.
Overview of Geothermal Energy
Geothermal energy originates from the Earth’s core and presents itself as heat that can be converted into electricity. The heat energy is typically accessed by drilling into underground reservoirs to tap steam and hot water that can drive turbines on geothermal power plants. Such energy is not only renewable but also reliable, unlike solar and wind energy which may fluctuate with daily and seasonal changes. The continuous availability of geothermal energy makes it a particularly enticing option for supplementing the world’s energy mix.
Importance of Effective Drilling for Geothermal Extraction
The efficiency of geothermal extraction heavily relies on the capability to drill accurately and reach the depths where hot fluids are available. Ineffective drilling can lead to significant financial losses and environmental risks. Therefore, precision in drilling to minimize impact, while maximizing the extraction, is crucial. It’s a complex task that demands a comprehensive understanding of geological conditions and the right drilling technology to match.
Key Components of Geothermal Drilling Systems
Drill Rigs
Geothermal drilling rigs are massive structures designed for extreme depths and high-temperature conditions. These rigs are equipped with rotary tables or top drives that provide the torque necessary to turn the drill string, along with drawworks for hoisting. Modern rigs are often automated and capable of high-speed drilling, with safety interlocks to prevent dangerous situations. The choice of a drilling rig can affect the efficiency and safety of the entire drilling operation.
Downhole Tools
Downhole tools play a critical part in drilling operations. They include drilling jars that help in dislodging stuck drill bits, heavy-weight drill pipe for additional downward force, stabilizers that ensure the straightness of the wellbore, and reamers that enlarge the diameter of the wellbore. All these tools must withstand extremely high-pressure and temperature conditions found in geothermal wells.
Drilling Fluids
Drilling fluids or muds are circulation mediums used to carry rock cuttings to the surface, cool and lubricate the drill bit, and maintain hydrostatic pressure to prevent formation fluids from entering the wellbore. Geothermal drilling fluids have to be specially formulated to withstand high temperatures and must not react with the rock formations or reduce the permeability of the geothermal reservoir.
Advanced Drilling Technologies
Enhanced Drilling Techniques
The complexity of geothermal drilling has led to the development of enhanced techniques aimed at increasing penetration rates and operational efficiency. These encompass the use of polycrystalline diamond compact (PDC) cutters, rotary steerable systems, and managed pressure drilling. Such technologies provide better control over the drilling direction and speed, essential for accurately targeting geothermal reservoirs while maintaining well integrity.
Directional Drilling and Measurement While Drilling (MWD)
Directional drilling is vital in tapping into geothermal resources that might not be positioned directly beneath the drilling site. This approach allows operators to steer the well path to optimize production from the geothermal reservoirs. Alongside directional drilling, MWD technologies are employed to provide real-time data on the well’s trajectory and geological formation properties, which is imperative for prompt and precise decision-making during drilling operations.
Drill Bits: The Cutting Edge of Geothermal Drilling
Types of Drill Bits
Different geological formations call for different drill bit types, and in the geothermal industry, the choice often falls between roller cone bits and fixed cutter bits. Roller cone bits are suitable for softer formations, while fixed cutter bits, particularly PDC, are used for harder, more abrasive rock. The selection of the appropriate bit is critical in optimizing drilling efficiency and minimizing downtime.
Material Advancements and Design Innovations
Drill bit technology has significantly evolved with new materials and design innovations aimed at increasing their lifespan and effectiveness. Advanced materials such as synthetic diamonds and harder metals have vastly improved the wear resistance of drill bits. Furthermore, design features like strategic cutter placement and hydraulic efficiency innovations play a substantial role in reducing bit trips and drilling time.
Drilling Fluids and Additives
Purpose and Function of Drilling Fluids
Drilling fluids serve multiple purposes, from cooling and cleaning the drill bit to stabilizing the wellbore walls and controlling formation pressures. They are an integral part of any successful drilling process, especially in the high-stress conditions of geothermal drilling where thermal degradation of fluids can be a significant issue.
Types of Drilling Fluids and Their Applications
The primary types of drilling fluids include water-based, oil-based, and synthetic-based muds. Water-based muds are widely used due to their lower cost and ease of handling, but in geothermal drilling, the use of oil-based and synthetic-based muds can offer superior thermal stability and rock-cutting carrying capabilities.
Additives for Improved Performance
Various additives are mixed into drilling fluids to enhance their performance characteristics. These can range from weight materials like barite to control wellbore pressure, to viscosifiers and fluid loss control additives that maintain the integrity of the fluid under extreme conditions. The precise formulation of additives is often a closely guarded secret of drilling companies.
Casing and Cementing Equipment
Importance of Casing in Geothermal Drilling
Casing is used to line the wellbore of geothermal wells, providing stability to the wellbore walls and preventing contamination between underground fluids and freshwater zones. Well casings have to be incredibly robust – they face high temperatures, pressures, and corrosive elements from the geothermal fluids.
Types of Casing Pipes
Various types and sizes of casing pipes are used, depending on the depth and diameter of the well. There are conductor casings, surface casings, intermediate casings, and production casings, each with specific functions, from protecting shallow water tables to providing a conduit for geothermal fluid extraction.
Cementing Technology and Equipment
Proper cementing of the casing into place is critical for ensuring the well’s structural integrity and isolating different underground zones. High-temperature cements and advanced cementing tools are necessary to withstand the demanding conditions of geothermal wells. The cement has to set successfully in the high-heat environment and maintain its seal over the life of the well.
Blowout Preventers and Safety Systems
Role of Blowout Preventers (BOPs)
Blowout preventers are essential safety devices designed to seal, control and monitor wells to prevent blowouts – the uncontrolled release of formation fluids. In geothermal drilling, the BOPs must be able to cope with extreme temperatures and pressures and be capable of quick activation in emergency situations.
Safety Systems and Emergency Shutoffs
Besides BOPs, comprehensive safety systems comprise several layers of backups, such as emergency shutoffs and automated alarms. These safety systems are integral to protecting both personnel and equipment and minimizing environmental risk in the event of equipment failure or other drilling anomalies.
Monitoring and Control Systems
Real-time Monitoring Technologies
Real-time monitoring encompasses a suite of technologies that constantly gauge various parameters within the drilling operation. These systems provide data on pressures, temperatures, and equipment status, and are crucial for prompt responses to changing well conditions. They are the eyes and ears of the drilling operation, affording operators a detailed view of the subsurface environment.
Automated Control Systems and Software
Automated control systems and specialized software contribute to the efficiency and safety of geothermal drilling operations. These systems can automatically adjust drilling parameters based on real-time data, optimizing drilling performance and reducing human error. Integration with MWD tools ensures that the drilling path stays on course, and deviations are corrected promptly.
Maintenance and Repair of Geothermal Drilling Equipment
Routine Maintenance Strategies
Robust maintenance strategies are pivotal for ensuring geothermal drilling equipment operates correctly and safely. Regular inspections, testing, and servicing are necessary to prevent mechanical failures and maintain operational capacity. Preventive maintenance routines also extend the lifespan of the expensive drilling equipment and tools, ensuring they remain in serviceable condition.
Repair Techniques for Geothermal Drilling Tools
When tools and equipment do fail, having efficient repair techniques in place minimizes downtime and ensures that operations can resume swiftly. This often involves on-site repair capabilities and replacement part inventories. Advanced diagnostic tools help quickly pinpoint issues so repairs can target the exact problem areas, saving time and resources.
Future Trends and Innovations in Geothermal Drilling Technology
Research and Development in Drilling Tools and Techniques
Continuous improvements in geothermal drilling are emerging from ongoing research and development efforts. Future drilling tools may see further enhancements in materials science, providing even more robust and long-lasting tools that can decrease operational costs and improve success rates.
The Role of Renewable Energy Policies in Shaping Drilling Technology
Pushes for renewable energy sources have incentivized advancements in geothermal drilling technology. Policymakers and industry stakeholders are increasingly understanding the value of drilling technologies that can tap into the Earth’s thermal energy more efficiently and sustainably, driving investment and innovation in the sector.
The quest for advanced tools and technologies is critical in the pursuit of effective geothermal drilling practices. These systems not only reduce environmental impact but also contribute to the secure and efficient harnessing of geothermal resources, which are set to play an increasingly important role in the global energy portfolio. In conclusion, as the industry progresses, effective drilling facilitated by state-of-the-art technology will be at the heart of geothermal energy extraction. As such, the ongoing evolution of geothermal drilling equipment and methods will remain a pivotal area of focus in the energy sector.