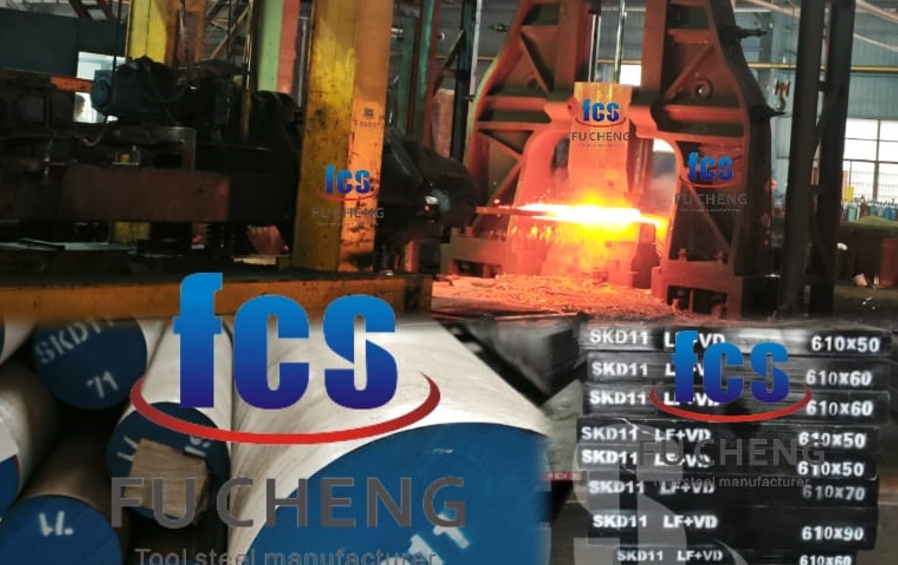
The manufacturing industry prefers SKD11 steel as its primary material for dependable, high-performance precision stamping dies production. Modern production needs SKD11 high-carbon, high-chromium tool steel to resist change and have minimal upkeep requirements.
This article looks at SKD11 steel applications in stamping dies and explains selection approaches for peak performance alongside necessary maintenance techniques to reach long life and operational excellence.
What is SKD11 Steel?
The Japanese Industrial Standards classify SKD11 steel as an advanced cold-worked tool steel. The composition of AISI D2 steel equivalent SKD11 combines approximately 1.5% Carbon with 12% Chromium. The elements deliver superior compressive strength, exceptional resistance to wear, and high hardness properties.
SKD11 serves purposes in die-making as well as cutting tools and industrial blades due to its capability to maintain toughness while delivering high hardness and perform well under demanding precision and stress requirements.
The applications of SKD11 Steel in precision stamping dies require evaluation
The manufacturing process of precision stamping consists of making complex metal parts through specific shape-pressing methods. Production requires materials that resist high-pressure operations, repeated impacts, and extended production durations.
SKD11 steel finds its primary applications in precision stamping dies for several purposes, including blanking dies, punching tools, and forming tools.
1. Blank Dies and Punching Tools
The hard nature of SKD11 steel makes it ideal for use in forming tools such as punches and blanking applications. The steel produces neat cuts while protecting tool life across production runs by precisely maintaining dimensions.
2. Forming Dies
When used in forming operations, SKD11 maintains a constant structural condition in the die because it offers resistance to change in shape. Production runs at high repeatability levels because SKD11 steel will not deform under stress.
3. Coining and Embossing Dies
To perform at high pressure, the die needs sufficient mechanical strength. The compressive properties of SKD11 allow it to deliver refined and precise impressions through contact points without sustaining damage such as breakage or fracture.
4. Bending Dies
The rugged yet tough properties of SKD11 deliver advantageous performance to bending dies, which support flexible metal shaping capabilities.
Why Choose SKD11 Steel for Stamping Dies?
The correct material selection for stamping dies is essential to achieve optimal efficiency and quality performance. These are the main reasons why producers select SKD11 steel:
1. High Wear Resistance
The material exhibits remarkable durability against scraping forces and material sticking effect, particularly in cases where complex or coated objects enter the operation.
2. Stable Heat Treatment
Steel components keep their dimensions after heat treatment, so secondary machine adjustments are unnecessary.
3. Good Machinability
SKD11 becomes straightforward for machine operations when annealed, despite maintaining its hardness rating. The material enables manufacturers to produce complicated die shapes with accurate dimensions.
4. High Toughness
Factors contributing to sudden failure or cracks must show high resistance under multiple load cycles. SKD11 meets this demand well.
How to Select SKD11 Steel for Your Dies?
Multiple factors must be evaluated before you choose SKD11 steel for your stamping needs.
1. Type of Operation
The most suitable condition for SKD11 steel tools used for cutting or blanking operations is in its fully hardened state. The formation and bending processes require steel with lower hardness since reduced brittleness leads to improved performance.
2. Thickness and Material of Workpiece
The resistance to material wear from thick and abrasive stamped components makes SKD11 a vital choice in such applications.
3. Expected Production Volume
The high-volume production benefits from SKD11 because the material provides essential durability to minimize production interruptions and reduce tool replacement needs.
4. Surface Treatments
To achieve better results, you should apply nitriding solutions or PVD coatings on the surface, enhancing lubrication benefits alongside friction minimization.
Maintenance Tips for SKD11 Stamping Dies
The best tool steel needs periodic maintenance to reach its maximum lifespan. You can maintain excellent conditions of your SKD11 steel dies by following these instructions:
1. Regular Cleaning
Maintain the dies free of all debris, together with workpiece residue. The presence of accumulated residue leads to wear discrepancies, which affect operational capabilities.
2. Lubrication
High-quality lubricating substances should be used during high-speed operations to minimize heat buildup and friction.
3. Inspection and Polishing
Checking for surface wear and cracks during regular inspections enables quick discovery of necessary remedial work. Surface smoothing, requiring light polishing, helps improve die precision.
4. Controlled Storage
Dry stored SKD11 dies must remain in controlled temperature rooms that protect them from corrosion and thermal damage.
5. Re-hardening if Needed
Suppose your device requires performance restoration after continued usage. In that case, you can rebuild its surface by re-hardening or regrinding before pursuing complete replacement.
Where to Buy Quality SKD11 Steel?
Finding reliable SKD11 steel requires customers to select suppliers that demonstrate reputation excellence in quality production and uniformity. The leading tool/mould steel factory known for industrial materials distribution is FCS Steel, which provides premium-grade materials to customers. FCS Steel delivers perfectly processed SKD11 steel that satisfies international quality benchmarks, a pledge for precision and durability, and excellent customer service.
The steel products supplied by FCS Steel will deliver dependable performance with extended, helpful life for stamping dies and custom tool parts. FCS Steel stands as a trusted supplier to all manufacturers who pursue excellence.
Conclusion
The manufacturing of precision stamping dies achieves its best results using dependable SKD11 steel. Businesses from the automotive to electronic sectors depend on SKD11 steel because of its remarkable wear resistance, hardness, and dimensional stability properties. With their selection criteria and maintenance procedures, manufacturers who understand how to apply this material correctly can achieve longer die life while decreasing expenses and increasing production quality.
FAQs
Q1. Which industries rely on SKD11 steel for stamping die manufacturing needs?
A: The automotive sector and the electronics, aerospace, and appliances industries choose SKD11 steel for stamping components since it provides precision and strength.
Q2. When stamping dies, do dentists prefer SKD11 steel over D2 for their applications?
A: The choice of SKD11 over D2 depends mainly on market availability and regional industrial preferences, despite their matching composition and performance characteristics. The performance of both materials matches well when used for stamping operations.
Q3. Can SKD11 be welded?
A: The welding process of SKD11 requires proper attention for successful outcomes. The adequate combination of pre-heating, appropriate post-heat treatment, and filler materials prevents die cracking.
Q4. Under normal conditions, how many cycles can SKD11 stamping dies sustain?
A: Appropriate care and maintenance allow SKD11 dies to operate 100,000 to 1,000,000 manufacturing cycles under specific conditions.
Q5. What should be the appropriate hardness level of SKD11 when stamping applications?
A: The optimal performance during stamping occurs at 58–62 HRC when heat-treating SKD11 steel. The required hardness measure might differ based on the intended use of the die.