Businesses that deal with high quantities of goods must have efficient warehouse management systems, and conveyor systems are among the most effective ways to optimize operations. Automating product movement within a warehouse with conveyor systems drastically cuts down on human labor, improves accuracy, and speeds up procedures.
There are many different kinds of conveyor systems on the market and picking the appropriate one can have a significant impact on efficiency and organization. Various warehouse settings can be addressed by utilizing these technologies, which range from advanced Automated Guided Vehicle (AGV) systems to adaptable belt conveyors.
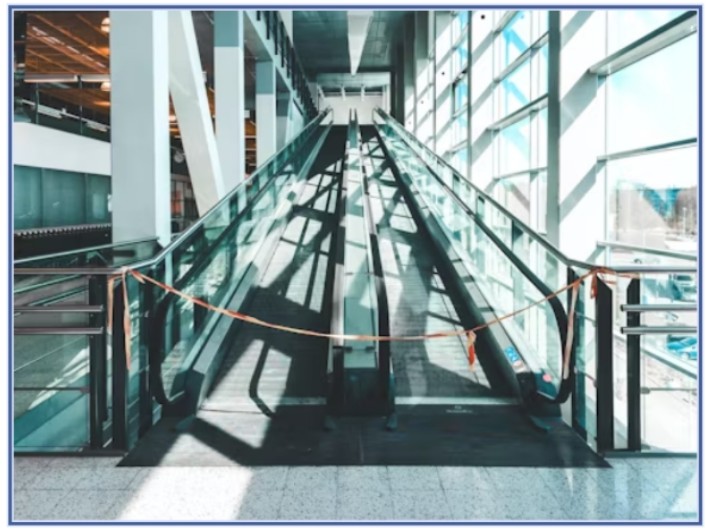
Read on to learn about the five best conveyor systems for warehouses and how they may improve management, workflow, and material handling for less waste and more money.
Why Conveyor Systems Are Crucial for Warehouses
In the modern, lightning-fast logistics industry, conveyor systems are crucial. There are several ways in which these systems improve the efficacy and efficiency of warehouse operations. For ten reasons, these are necessary:
- Maximized Efficiency: Automating the flow of items, conveyors drastically cut down on manual labor. As a result, firms can process more products in less time thanks to better throughput and faster processing times.
- Improving Precision: Human error is reduced when items are sorted and transported using automated processes. This enhances customer happiness and decreases returns by precisely placing and shipping merchandise.
- Enhanced Security: Workers are less likely to sustain injuries on the job because of conveyors, which automate the movement of large and heavy objects. There will be less downtime due to accidents and a safer workplace as a result of this.
- Optimal Use of Space: It is possible to optimize space utilization by designing conveyor systems. To increase storage capacity, vertical or installed above systems use vertical space that would otherwise go unused.
- Maximizing ROI: Despite the high cost of entry, these technologies pay for themselves in the long run through enhanced efficiency, decreased human error, and lower labor expenses.
- Efficiency in scaling: If your company expands, you can simply scale up or down conveyor systems. Conveyors are versatile enough to adapt to your changing needs, whether that’s an increase in product lines or an expansion of your warehouse.
- Regular Processes: To keep things running smoothly and without hiccups, these systems maintain a constant and steady flow of items through the several processing phases.
- Flexible Abilities: From individual items to full pallets, there is a conveyor type that can handle it all. Their adaptability makes them a good fit for a wide range of businesses, from distribution to retail to manufacturing.
- Saving Energy: By using state-of-the-art technology that minimizes power consumption and environmental effects, contemporary conveyor systems are engineered to be energy efficient.
- Keeping Tabs in Real Time: The ability to monitor and track items in real-time is made possible by integrating conveyors with warehouse management systems (WMS). Both inventory management and decision-making are aided by this.
Warehouse Conveyor Systems
Having a good understanding of conveyor systems will help you make better decisions regardless of the commodities your sector deals with. Within your current system, each conveyor provides a unique flow and level of productivity. Another option is to consult an expert who can design a custom conveyor system to meet your needs. Here are five typical conveyors that work well for moving materials around a processing plant.
1. Conveyors with Rollers
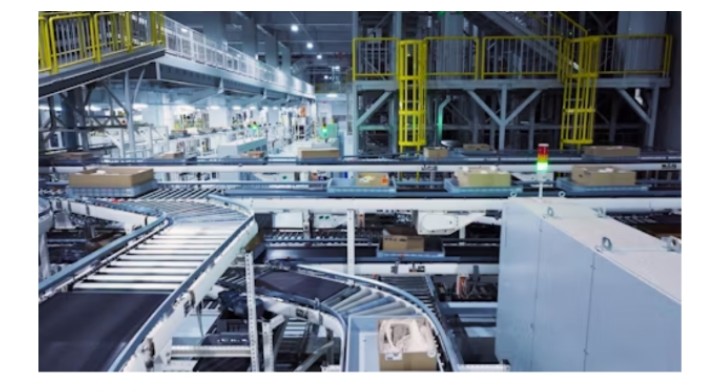
For transporting massive objects over level ground, nothing beats the adaptable roller conveyor, which can run on either electricity or gravity. Shipments involving large machinery, filled drums, loaded pallets, or hefty products are best handled by this material due to its durability, speed, and load capacity. A well-known type of roller conveyor, the chain-driven live roller (CDLR), is ideal for constantly transporting heavy objects over long distances and is hence popular in specific industries.
2. Conveyor Belts
The belt conveyor can simply and adaptably move a broad variety of warehouse goods due to its simplicity and adaptability. A closed-loop belt, often driven by two or more pulleys, efficiently moves items at a constant pace while keeping an even distance between them. The belt’s simplicity makes using a single drive for a wide range of product sizes, shapes, and weights possible.
You can adjust the conveyor’s height, swap out the belt for buckets or interlocking parts, or swap out the substance of the belt to meet traction requirements—all of which are specific to the needs of a warehouse environment.
3. Pallet Conveyors
The pallet conveyor, which can be either a roller or a belt, is ideal for transporting large, heavy items. It was meticulously designed to account for load capacity, pallet size, and automation levels, and it is vital for efficient handling of loaded pallets. For warehouses that demand mechanisms that can withstand repeated cycles and long-term usage, the pallet conveyor is an excellent choice.
4. Conveyors’ Overhead
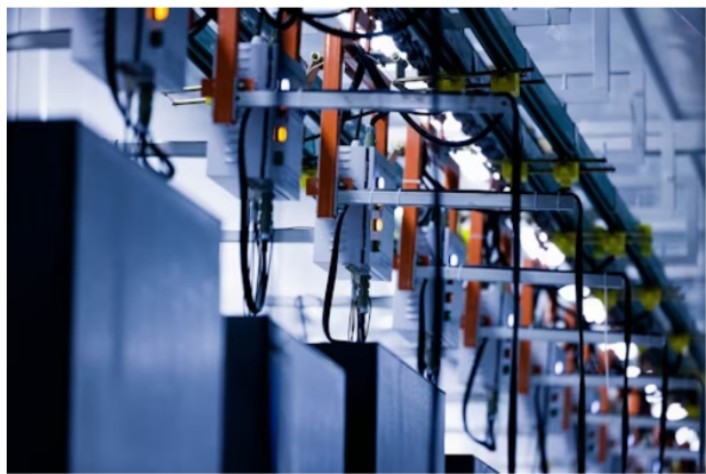
An overhead conveyor will work well in places where every square inch counts. Despite the complexity of the initial installation, the expenditure is well-justified by the system’s ability to utilize vertical space and manage heavy loads with variety. This conveyor is perfect for moving goods up and down aisles in a warehouse, freeing up space for storage, machinery, and other essentials by keeping them off the floor.
5. The Versatile Conveyors
A flexible conveyor can be easily installed in any region that has limited space. The rotator conveyor is one such device; it can shift the product’s direction while keeping complete control over it. The flexible conveyor is a popular and innovative option for moving items around a warehouse because of its adaptability, mobility, and space-saving design.
Another illustration is the low-profile conveyor, which is both a space-saving and aesthetically pleasing device that can integrate seamlessly into an existing system while yet meeting the continuous demands placed upon it.
Additional Considerations:
Choosing the correct system has a big influence on operational performance. Consider numerous other pieces of information, as well as the essential feedback of conveyor engineering professionals, to help you make an informed selection.
Robotics and Safety
The constant development of technology contributes to the growth of robots for conveyor systems. As software is incorporated into each system’s mechanism, real-time tracking and controls have become industry standard. At the very least, employing technology and robots in conveyor systems minimizes the need for personnel in warehouse environments where human skills may be better utilized elsewhere.
In the end!
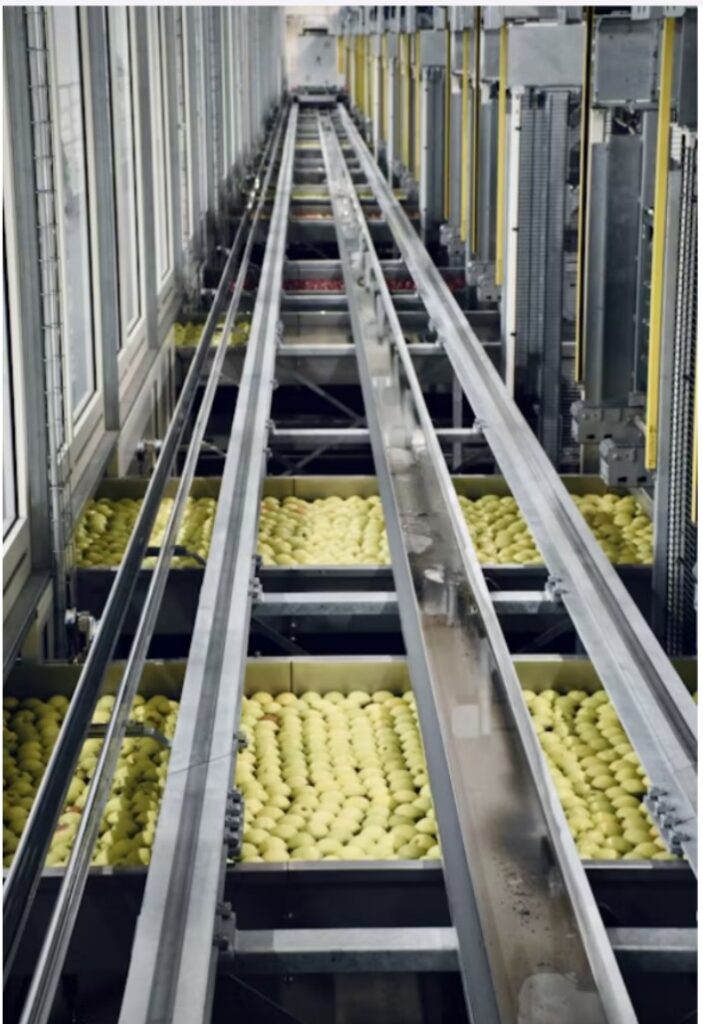
Finally, with their many advantages, including higher productivity and enhanced safety, conveyor systems are crucial for effective warehouse management. A conveyor system can help you achieve your goals of improving material flow, automating sorting, or making better use of available space. Investing in the correct conveyor technology can help you save money, simplify your processes, and run your warehouse like clockwork.